Fixed Bed Process Hydrogen Peroxide
There are several methods for hydrogen peroxide production and manufacturing, among them the
AO(auto-oxidation) process is the most prevailing one. In this process, 2-alkyl
anthraquinone is mixed with organic solvent to make up the working solution,
which is hydrogenated in presence of catalyst, and the resulting is oxidized by
air (or oxygen) in counter-current way before being extracted, regenrated,
purified and enriched to get commercial hydrogen peroxideproduct. Depending upon
the different reactor type in the hydrogenation unit, AO process is further
divided into Fixed Bed Reactor Process and Fluidized Bed Reactor Process.
Introduction of Anthraquinone Method
At present, the industrial production of hydrogen peroxide in the world basically uses anthraquinone method (this method was started by DuPont Company in 1953), which takes alkyl anthraquinone as the working carrier.
In China, 2-ethyl anthraquinone(EAQ)is mainly used as the working carrier. Dissolve EAQ in organic solvents(generally composed of heavy aromatics and trioctyl phosphate (TOP) in certain proportion) to form working fluids, hydrogenation and oxidation are then carried out under the action of catalyst (palladium catalyst) to produce hydrogen peroxide (H2O2) and H2O2 is extracted from the working fluid with pure water to obtain hydrogen peroxide with H2O2 content of 27.5%, which is concentrated and reprocessed into other specifications.
SL Tec is a leading supplier of technology and turnkey solutions and services for hydrogen peroxide manufacturing and hydrogen peroxide production plants. SL Tec provides both fixed bed reactor process and fluidized bed reactor process. The fixed bed reactor process SL TEC provides is the
most advanced technology in China. It employs heavy aromatics-TBU-TOP tertiary
solvent in the working solution and alumina-supported Pd catalyst with high
activity. Learn more
Welcome to contact us to get professional guidance for hydrogen peroxide production cost for gydrogen peroxide plant.
You May Also Like
●How Is Hydrogen Peroxide Made?
●New Process Can Deliver Hydrogen Peroxide In Remote Areas
●Hydrogen Peroxide Can Be Used As a Sterilant
●Is Hydrogen Peroxide Useful For Treating Water Pollution?
●Hydrogen Peroxide Plant Supplier Shares Knowledge About Hydrogen Peroxide
Features of Fixed Bed Process Hydrogen Peroxide
The fixed bed hydrogenation reactor setup for hydrogen peroxide production, specifically the technology offered by SL TEC, boasts several advantages over other fixed bed reactor processes prevalent in China. Here are the key features of this hydrogen peroxide process:
Advanced Control and Safety Systems
The fixed hydrogen peroxide system incorporates an advanced Distributed Control System (DCS), a Safety Instrumented System (SIS), and an industrial video monitoring system.
This setup ensures optimal control, alarms, and safety interlocks for various process parameters during the hydrogen peroxide production process, resulting in a stable, high-yield, low-cost, and safe operation.
Efficient Distillation Technology
The concentration of hydrogen peroxide utilizes cutting-edge hydrogen peroxide distillation technology through falling film distillation.
This method minimizes the residence time of the hydrogen peroxide solution in the evaporator, preventing decomposition of the product.
Additionally, low-pressure saturated steam is employed to maintain an effective temperature difference of 8 to 10 °C, which conserves steam consumption and reduces unit costs.
Effective Wastewater Treatment
Centralized Emission Management
The system features a centralized air release mechanism for recovering and disposing of unorganized exhaust gases.
This innovation eliminates onsite odors, reduces solvent consumption, enhances the working environment, and meets occupational health and environmental protection standards.
Enhanced Drying Column Design
The post-treatment drying column employs high-efficiency reaction and separation filler packing.
This design resolves issues related to alkali formation in the drying column and alleviates the burden on subsequent activated alumina beds, thereby reducing their consumption while ensuring long-term operational stability.
High-Efficiency Purification
A purification column utilizing high-efficiency oil-water separation coalescing fillers significantly lowers organic carbon content in the final product.
This ensures that the organic carbon levels meet high-end user requirements without necessitating further purification.
Tail Gas Recovery Process
The treatment of tail gas employs a high-efficiency solvent recovery process that combines turbo expansion refrigeration with carbon fiber adsorption recovery.
This innovative approach allows for the recovery of up to 80% of solvents from low-temperature exhaust gases, thereby extending the lifespan of activated carbon fibers and minimizing regeneration frequency.
Optimized Extraction Technology
The high-efficiency extraction column ensures optimal oil-water separation and extraction technology, achieving high extraction concentrations with minimal raffinate waste.
The design allows for stable production of hydrogen peroxide with concentrations exceeding 35%, while reducing extraction column volume by 20% compared to conventional processes.
Advanced Oxidation Column Design
Utilizing a gas-liquid mixed high-efficiency oxidation column enhances the thorough mixing of oxidizing working fluids with air oxygen.
This design has been successfully applied in multiple equipment setups, achieving an oxidation collection rate exceeding 98%.
Cost Efficiency
The overall production costs are nearly halved compared to traditional methods.
The SL TEC oxidation system employs advanced operational techniques to lower oxidation operating pressures while maintaining yield efficiency.
For instance, the outlet pressure for air compressors has been reduced from 0.5–0.6 MPa to 0.40–0.45 MPa, yielding a 20% energy saving.
Superior Catalytic Performance
The palladium catalyst used in the hydrogenation reaction exhibits high catalytic activity and exceptional selectivity for cesium hydrogenation.
This results in reduced enthalpy consumption—less than 0.2 kg per ton of product (27.5% concentration)—which is one-fifth of the industry average, leading to significant reductions in overall chemical raw material consumption.
These features collectively position SL TEC's fixed bed hydrogenation reactor setup as a leading technology in the efficient production of hydrogen peroxide, emphasizing sustainability and cost-effectiveness while maintaining high safety standards.
Transform your production process and reduce costs significantly! Get in touch with SL Tec today and learn how our advanced solutions can benefit your business!
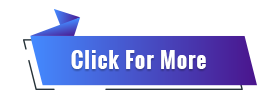
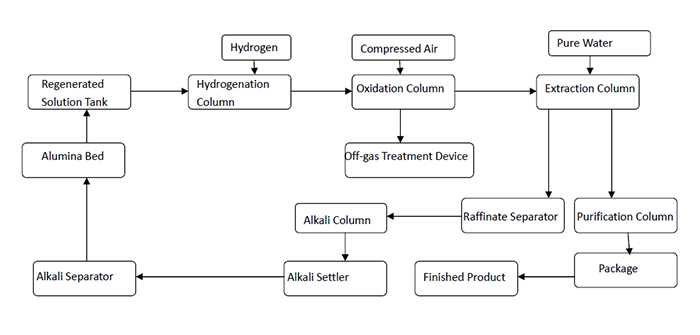
None
None