Fluidized Bed Process Hydrogen Peroxide
There are several methods for hydrogen peroxide production, among them the
AO(auto-oxidation) process is the most prevailing one. In this process, 2-alkyl
anthraquinone is mixed with organic solvent to make up the working solution,
which is hydrogenated in presence of catalyst, and the resulting is oxidized by
air (or oxygen) in counter-current way before being extracted, regenrated,
purified and enriched to get commercial hydrogen peroxideproduct. Depending upon
the different reactor type in the hydrogenation unit, AO process is further
divided into Fixed Bed Reactor Process and Fluidized Bed Reactor Process. SL Tec
provides both processes.
For this hydrogen peroxide production technology, SL TEC cooperates with one of the branch companies of China National Chemical Engineering Co., Ltd.—— SEDIN Ningbo Engineering Co., Ltd. to offer a turnkey hydrogen peroxide plant.
The Fluidized Bed Reactor Process SL TEC offers uses heavy aromatics-TBU
binary solvent in the working solution(WS) system, with the WS capacity
(H2O2-kg/m3-WS) reaching 12g/L.
You May Also Like
●How Is Hydrogen Peroxide Made?
●New Process Can Deliver Hydrogen Peroxide In Remote Areas
●Hydrogen Peroxide Can Be Used As a Sterilant
●Is Hydrogen Peroxide Useful For Treating Water Pollution?
●Hydrogen Peroxide Plant Supplier Shares Knowledge About Hydrogen Peroxide
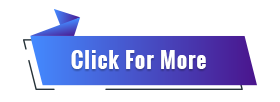
Advantages of Fluidized Bed Process Hydrogen Peroxide Manufacturing Plant
● Hydrogen Peroxide Manufacturing Plant enables much larger production capacity, i.e. over 200,000TPA as per
100% hydrogen peroxide for one production line.
● The WS capacity of Hydrogen Peroxide Manufacturing Plant is as high as 12g/L; 35-40% hydrogen peroxide can be
directly collected from the extraction column; the total yield reaches up to
97%.
● Both material consumption and energy consumption are reduced, thereby the
production cost of Hydrogen Peroxide Manufacturing Plant is lower.
● Due to the absence of potassium carbonate drying column and relating
control problems, the process flow of Hydrogen Peroxide Manufacturing Plant is shorted, the product quality is better and
more favorable for the production of high purity hydrogen peroxide, like food
grade and electronic grade.
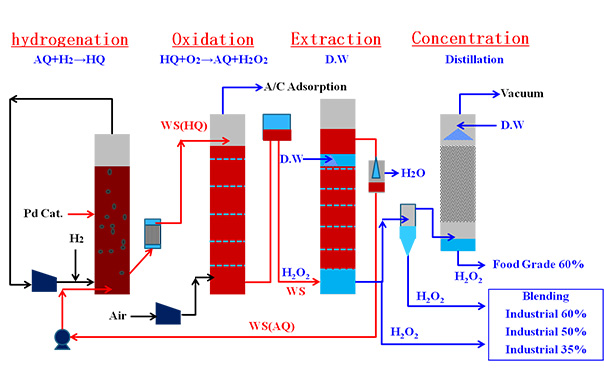
Hydrogen Peroxide Manufacturing Plant Process Flow Description
1.Hydrogenation Unit
The working solution (WS) is pressurized and enters into the WS Temperature conditioner before being charged to the bottom of the hydrogenation column with Pd catalyst; fresh hydrogen from the surge tank is filtered and combined with the recycling hydrogen from the hydrogen compressor before entering the bottom of the hydrogenation column. The WS and hydrogen flows up in a co-current way, part 2-EAQ is hydrogenated to HEAQ, and the non-reacted hydrogen flows from the hydrogenation column to the separation and cooling unit before mixing with the fresh hydrogen and enters into the hydrogenation column again.
The hydrogen and the hydrogenated solution goes through gas-liquid separation, and the resulting hydrogenated solution is filtered, cooled and fed to the hydrogenated solution storage tank. While the filtered Pd catalyst powder is re-flushed by the re-flushing liquid into the bottom of the hydrogenation for re-use.
The hydrogenated solution in the storage tank is pressurized, and goes through two-stage filters to avoid the entering of the catalyst powder into the hydrogen peroxide solution and causing any possible mistake.
2.Oxidation Unit
The oxidation column consist of air distributor, re-distribution plate, distribution cooler and packings. In this column, the hydrogenated solution from the last step is oxidized and the oxidation solution is obtained. The off-gas obtained from gas-liquid separation is cooled and condensed to get the mixture of aromatic and water before entering into the off-gas recovery cooler to have heat exchange with the low temp. oxidation gas from the expander. The heat exchanged off-gas enters into the off-gas recovery tank to separate out the condensed aromatic, which is to be recovered.
3.Extraction and Purification Unit
3.1 Extraction and Purification of Hydrogen Peroxide
The oxidation solution from the oxidation unit overhead tank is sent to the lower part of the extraction column, and dispersed into numberless globule and float to the column top; at the same time, the pure water from the overhead tank is heat exchanged to increase the temp. and charged to the extraction column upper section to have counter-current extraction with the upwards floating oxidation solution. The crude hydrogen peroxide is obtained at the bottom of the extraction column, while the resulting oxidation solution flows out of the extraction column top and enters into the working solution coalesce and the working solution water separator.
The crude hydrogen peroxide is fed to the purification full with aromatic which flows from the purification column overhead tank to have counter-flow contact to remove the organic impurities in the hydrogen peroxide, and the resulting hydrogen peroxide intermediate flows out of the purification column bottom, while the heavy aromatic from the top is charged to the used aromatic storage tank.
3.2H3PO4 Solution Make Up and Adding H3PO4 Solution into Pure Water
3.3Automatic analysis of oxygen content at the extraction column top and the purification column top and heavy aromatic vapor dilution by nitrogen
3.4Working solution vacuum drying
4.Re-generation Unit
During the hydrogenation and the oxidation, small amount of anthraquinone degrading compounds will be generated; to reduce the consumption of the EAQ consumption and keep the cleanness of the working solution, part of the hydrogenation solution or the recycling working solution shall be introduced to the alumina oxide bed for regeration.
None