At present, the domestic methanol plant to coal as raw material, the use of coal gasification of methanol. The methanol synthesis step is carried out by compressing the fresh feed gas from the low temperature methanol and carrying out the catalytic reaction in the methanol synthesis column to produce the crude methanol product and then producing the qualified alcohol by distillation. A small amount of fusel oil mostly directly into the fusel oil tank for sale, not fully utilized. If through my company's technological transformation, fusel oil can be fully utilized, and can produce good social and economic benefits.
Domestic coal chemical fusel oil treatment in two ways, namely, fuselage oil intermittent evaporative recovery and recovery of fusel oil continuous distillation.The former is intermittent operation, the size of fusel oil treatment is limited; The latter is through the provision of a methanol recovery column to recover methanol, while the preparation of C2-C6 alcohol fractions, the drawback is that the fine methanol is still containing more impurities, generally only as a low-grade products.
In view of the above problems, our company relies on years of experience in chemical separation and customization, we using pressurized distillation and atmospheric distillation of the coupling method. Not only the top of the distillation column can be achieved to meet the national standard of high quality pure methanol, but also atmospheric distillation column using pressurized distillation column top material as a heat source, energy utilization has been greatly improved. More importantly, my company's matching fusel oil wastewater treatment process uses a two-step advanced oxidation and composite membrane - bioreactor (Membrane Bio-Reactor, MBR) in a combination of ways to meet ("petrochemical industry pollutants Emission standards "GB31571-2015) direct discharge standards and recycling water reuse standards, to solve the customer's worries.
SL TEC has the mature and reliable technology for the fusel oil separation technology. Please contact with us if you have such demand.
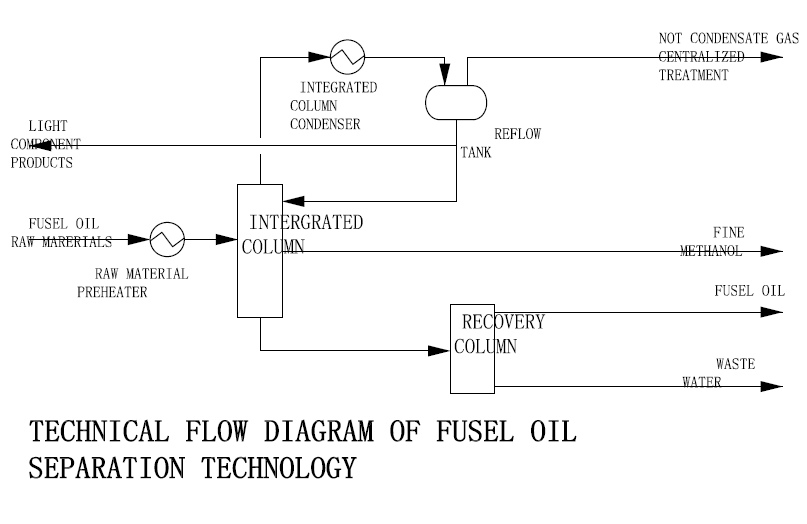
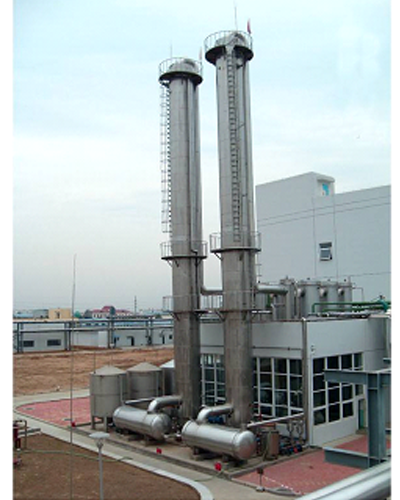
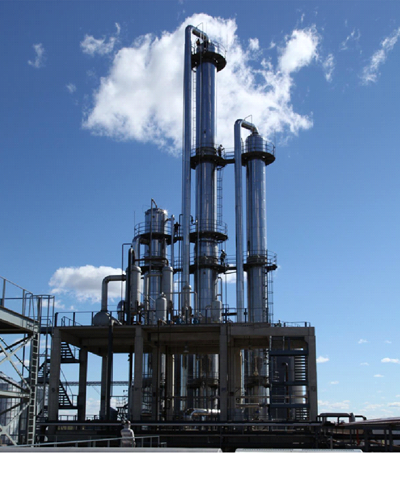
1.Processing capacity: 100,000 tons / year fusel oil;
2.Run time: 8000 hours / year;
3.Operational flexibility: 60-120%;
4.Raw materials:
S/N | Component | unit | content |
1 | Light component | % wt | 1.00 |
2 | Methanol | % wt | 62.59 |
3 | Ethanol | % wt | 1.70 |
4 | Propanol | % wt | 0.84 |
5 | N-butanol | % wt | 0.44 |
6 | N-amyl alcohol | % wt | 0.20 |
7 | Isoamyl alcohol | % wt | 0.12 |
8 | 2-heptanone | % wt | 0.08 |
9 | 2-butyraldehyde | % wt | 1.39 |
10 | water | % wt | 31.39 |
11 | benzene | % wt | 0.26 |
12 | total | % wt | 100 |
5.The main products:
S/N | product name | specification | unit | Capacity |
1 | Fine methanol | See product a technical indicators * | t/a | 50095 |
2 | Fusel oil | See product two technical indicators * | t/a | 26270 |
* Product a technical indicators: methanol
S/N | Item | Unit | index |
1 | Methanol | % wt | 99.95 |
2 | Ethanol | % wt | 0.05 |
* Product two technical indicators: fusel oil
S/N | Item | Unit | index |
1 | Light component | % wt | 3.87 |
2 | Methanol | % wt | 48.31 |
3 | Ethanol | % wt | 6.47 |
4 | Propanol | % wt | 3.25 |
5 | N-butanol | % wt | 1.68 |
6 | N-amyl alcohol | % wt | 0.76 |
7 | Isoamyl alcohol | % wt | 0.46 |
8 | 2-heptanone | % wt | 0.30 |
9 | 2-butyraldehyde | % wt | 5.35 |
10 | water | % wt | 28.55 |
11 | benzene | % wt | 0.99 |
6.Utilities consumed (to treat fuselates containing 62.6% methanol per ton)
S/N | Item | specification | unit | Consumption |
1 | Circulating cooling water | 0.3Mpa(G),
32℃~40℃ | m3 | 92 |
2 | steam |
| t | 1.896 |
3 | Electricity |
| KWH | 20 |